Author: Jack Wang
Industry Demand Case Study:
Implantable devices like pacemakers require PCBs to withstand >500,000 bends over 10 years with a thickness ≤0.4mm. Traditional designs showed a 23% failure rate, making rigid-flex PCBs the breakthrough solution.
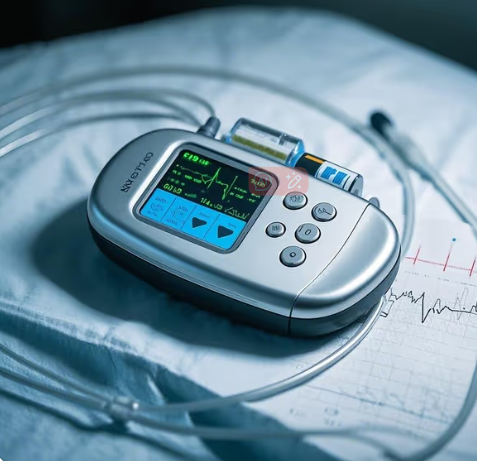
Key Technological Breakthroughs
1. Material System Innovation
① Substrate Selection:
Polyimide (PI) films offer 200× better bend resistance than FR-4 but cost 5× more. A balanced approach: Use PI (25μm thick) in bending zones and FR-4 in rigid areas.
② Adhesive Revolution:
Acrylic adhesive (300% elongation) outperforms epoxy resin (5% elongation) for dynamic bending. A glucose monitor project demonstrated a bend lifespan increase from 20,000 to 300,000 cycles.
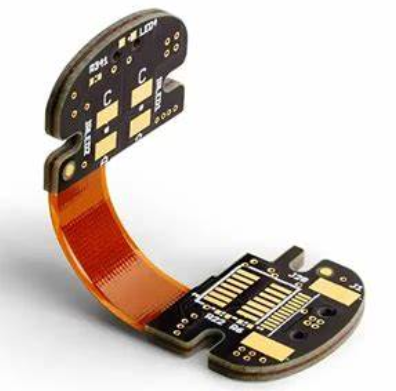
2. Bending Zone Design Guidelines
Minimum Bend Radius:
Formula: R = 100 × Copper Thickness (mm). Example: 35μm copper thickness → R = 3.5mm.
Trace Layout Rules:
→ No vias allowed in bending areas
→ Traces angled at 45° to bending direction reduce stress concentration by 60%
→ Grid-pattern copper etching improves flexibility by 3×
3. Reliability Validation Methods
① Accelerated Aging Test:
1,000 hours at 85°C/85% RH environment, impedance variation must remain <5%.
② Mechanical Fatigue Test:
Simulate human motion with servo motors (2Hz frequency, ±15° amplitude). Continuous 30-day testing with no fractures.
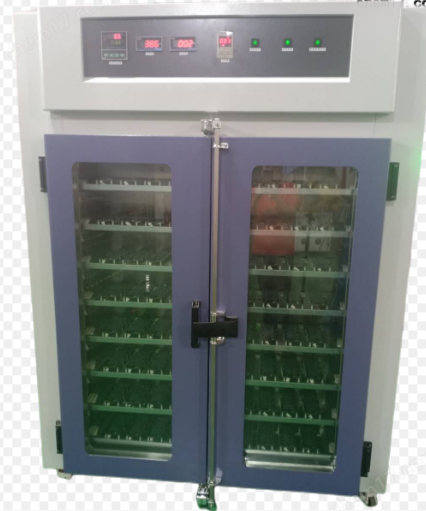
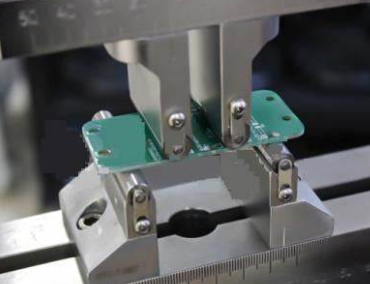
Typical Application Case
A neurostimulator using 6-layer rigid-flex design:
Rigid zones: 4-layer FR-4 for MCU and power modules
Flexible zones: 2-layer PI film for electrode array connections
Results: 0.35mm thickness, ISO 13485 certification, and 800,000-cycle bend lifespan.
If you want to know more, please feel free to contact us at www.pcbmaster.com
Author: Jack Wang